Reason #1: Planned Tasks Aren’t Getting Done Early
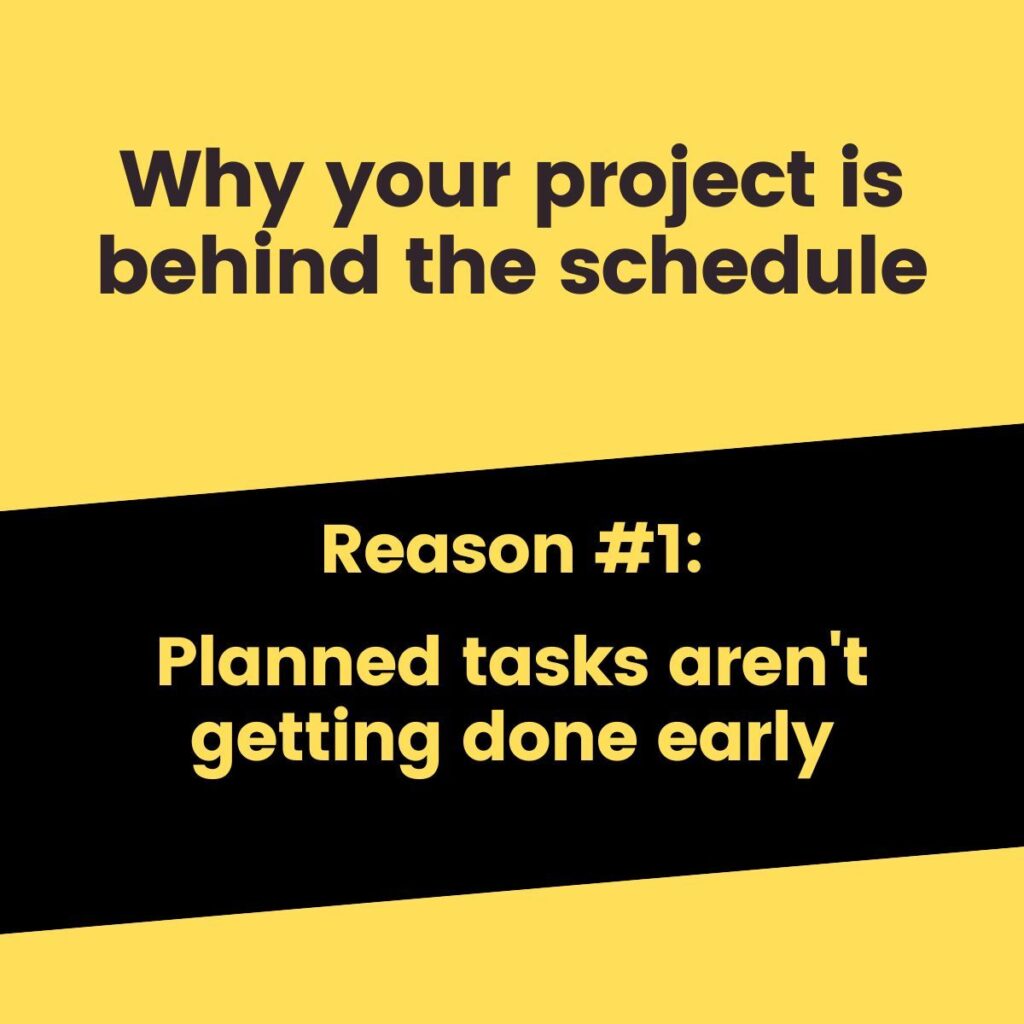
In the steel industry, projects often come with super tight deadlines that feel like mission impossible.
But surprisingly, in my experience, more than 90% of those “absolutely unrealistic” deadlines actually get met.
Sure, it often means burning the midnight oil, pulling in half the team, and using every trick in the book.
We might’ve gone a bit overboard with resources, but hey, the project was delivered on time!
On the other hand, I’ve noticed that even when projects have chillaxed deadlines, they still get handed in just a day or two before the final due date.
This paradox is called Parkinson’s Law:
đź’ˇ “Work expands to fill all the time allotted for its completion.”
C. Northcote Parkinson
For Example, if your project has two weeks for Shops Drawings Approval Review, you will receive Returned Approvals in 14 days, even if the work itself takes 3 days to complete.
If there is a Gantt chart on the wall that says that a task will take ten days, then the person who is assigned this work will try to stretch the job out for the full ten days.
Parkinson’s Law is very evident in RFI circulation.
I doubt that it takes more than two days to answer a simple question.
However, if the timeline for response is 10 working days, it is very unlikely to receive it before the end of the following week.
I bet loads of project managers in the steel industry can totally relate to the frustration of not hearing back for weeks.
The same thing may happen in the Detailing Office.
When a project has too much time in it, Detailers may start adding some bells and whistles to the drawings to avoid early completion.
But really, these extras aren’t needed, they’re just “embellishments.”
Some detailers are worried that if they finish the job too soon, the client might think they’ve been overcharged.
And there’s also this nagging fear that the client will expect them to always deliver ahead of time.
Parkinson’s Law is detrimental in itself, but it also exacerbates the effect of delay spread, which I am going to describe in the next chapter.
Reason #2: Delays Spread To Subsequent Stages Of The Schedule
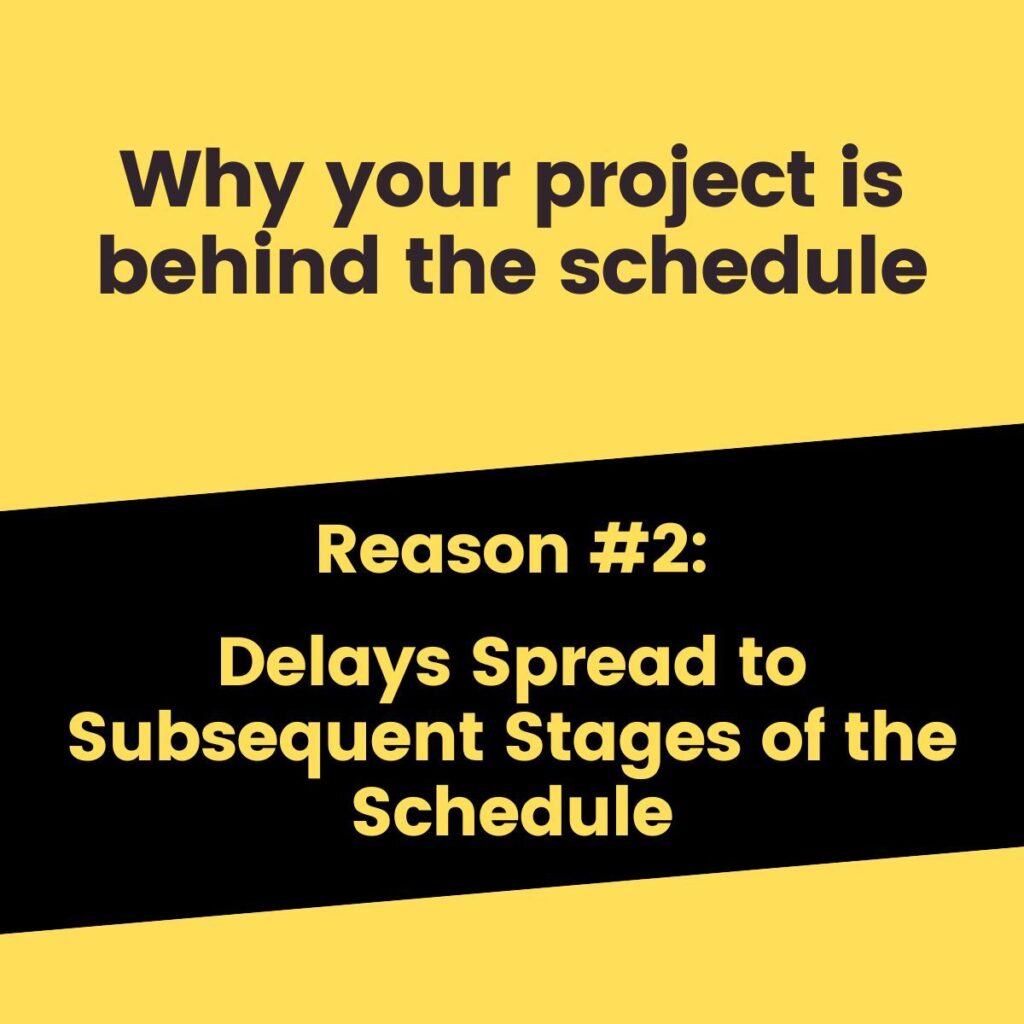
Frustrated by delays in your steel fabrication process?
Even in a simplified scenario, on-time production relies on a complex chain of events.
Never having been a steel fabricator, I admit that steel fabrication is a complex process.
However, to illustrate the concept of delay spread, let’s drastically simplify the process of steel fabrication.
Suppose I am a steel fabricator tasked with making beams and columns for a small commercial project.
In a very simplified scenario, to begin the fabrication, I need to:
1. Receive raw material from mill or service center;
2. Get a set of “For Construction” drawings from my detailer, after we receive the RA back;
Criteria for Early Start
The key point is that even in a simple case, early fabrication in the shop depends on the coincidence of ALL of the following events:
âś… The supplier delivers materials ahead of time;
âś… The detailer revises the shop drawings and releases them for construction ahead of schedule. But this also depends on getting approvals back in a timely manner.
âś… Shop workers become available to start work ahead of schedule.
A single failure can result in a delayed schedule.
If several conditions must be met for early fabrication to begin, ANY of the following events could be enough to delay the process:
❌ Materials are delayed on the way to the shop;
❌ The Detailer took a long time to make changes and release the Set For Construction
❌ The Detailer made changes in a reasonable timeline, but we received the Approvals too late;
❌ There are no available shop workers to process the steel;
In other words, a combination of conditions is necessary for an early start, and one reason is sufficient to delay the start.
The issue gets worse because, as mentioned before, jobs are hardly ever finished early.
This leads to late starts and the delay spreads to the later steps in the schedule.
Since finishing early is uncommon in general, processes like steel fabrication rarely start ahead of time.
In order to catch up on this backlog, Fabricators often force Detailers to break projects into sequences and work in inefficient “multitasking” mode, which I will talk about in the next chapter…
Reason #3: Multitasking Leads To Losses
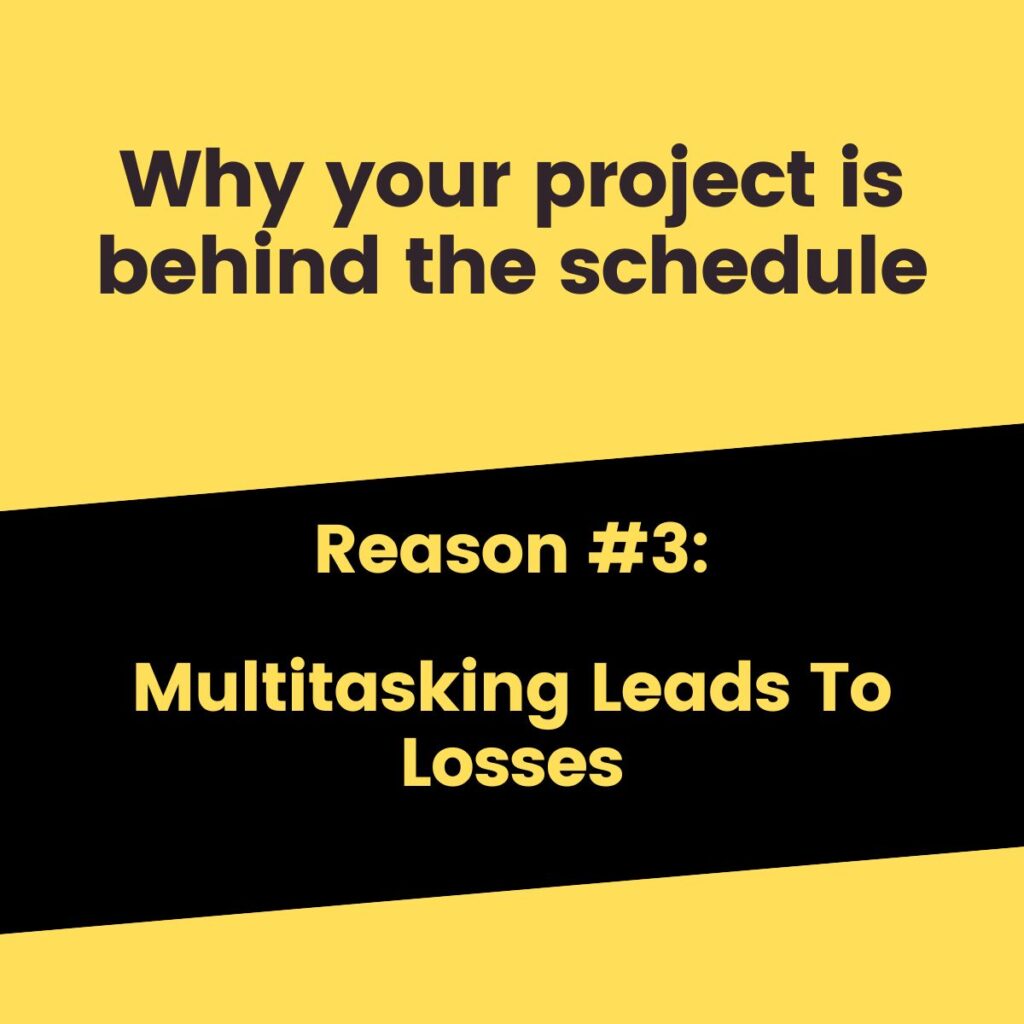
The third reason for the unsatisfactory results of traditional planning approaches is multitasking.
Or doing several tasks at the same time.
Multitasking is a Myth.
In fact, our brains are not wired to multitask. When we try to do multiple things at once, we are actually just switching back and forth between tasks very quickly.
This constant switching can lead to errors, decreased productivity, and increased stress.
“Multitasking” often becomes a problem when some parts of the project start to be completed late.
In this case, the interdependence between the types of work becomes critical.
Splitting Detailing Project may Backfire.
The fabricator, waiting for the completion of “For Construction” Drawings, starts asking the Detailer to provide him with at least a partial release so that he can start manufacturing.
Let’s say I have 12 days to issue drawings, of which I need to spend 4 days on modeling (M), 4 days on Erection Drawings (E) and 4 days on Piece Details (D).
To start earlier, the Fabricator asks me to release the project in 50/50 parts.
Now my schedule looks like this:
M(2d) → E(2d) → D(2d) → M(2d) → E(2d) → D(2d)
This often creates the illusion of speed, and everything looks smooth on paper.
But look, I will finish modeling 4(!) days later than planned. It is hardly worth doubting that this will affect the subsequent planned work.
The situation is aggravated by the fact that productivity decreases due to constant switching between tasks and projects.
It has been proven that when working with more than two tasks, productivity decreases significantly.
And when working with five tasks (not uncommon for Detailer), productivity can be only 25%, and the remaining 75% will be “switching losses”.
Switching = Losses.
If you are working on a task such as Steel Detailing, you have to keep dozens of circumstances in mind; remember the history of the project; understand what to do next; take into account all intra-project connections, and anticipate the difficulties that you may face.
A pretty difficult task.
What happens if you are interrupted or have to quickly switch to another task, even for an hour?
Your concentration is broken.
Now it may take hours of work just to get yourself back to the same state of concentration.
To understand how much switching affects our efficiency, do a simple test.
Try to pronounce the following sequence first horizontally, line by line. And then vertically: column by column.
And time how long it took you in each case.
A – 1 – Monday
B – 2 – Tuesday
C – 3 – Wednesday
…
G – 7 – Sunday
I spent 26 and 13 seconds respectively. And you?
About the Author:
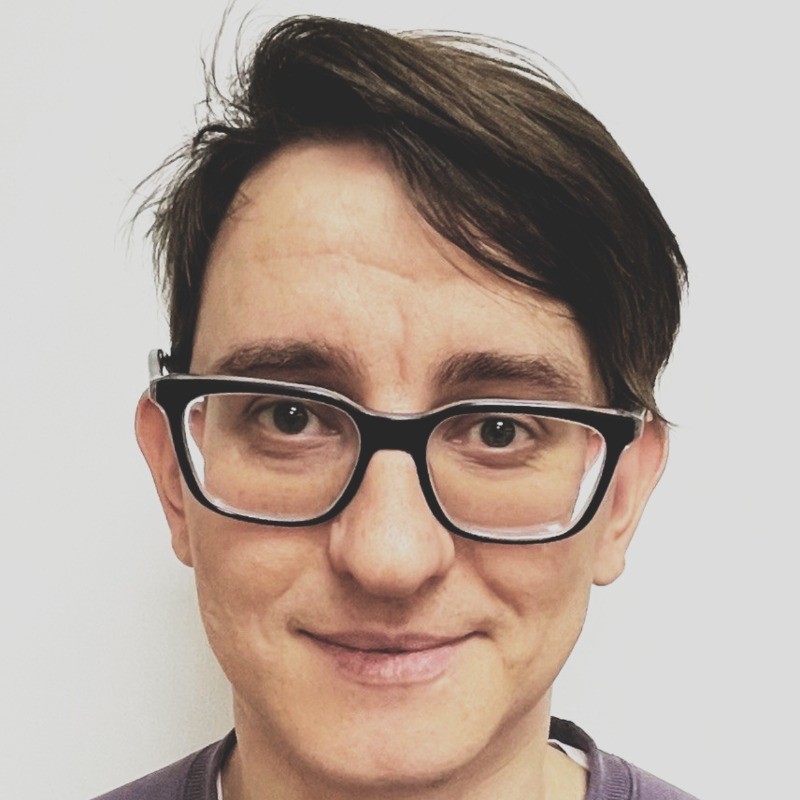
Igor Goriatchev – Owner & CEO at ESD Solutions. Helping Fabricators To Make Steel Real. We simplify steel detailing workflows and deliver accurate, error-free detailing solutions.